In the world of fluid handling, where safety, efficiency, and reliability are paramount, Pneumatic Double Diaphragm Pumps stand out as versatile workhorses. These pumps find application in a wide range of industries, from chemicals and pharmaceuticals to food and beverage, thanks to their ability to handle various fluids, including corrosive and abrasive ones. One of the standout features of these pumps is their impeccable sealing technology, which ensures zero leakage. In this blog, we will delve into the sealing technology that makes pneumatic diaphragm pumps leak-free champions.
Understanding Pneumatic Double Diaphragm Pumps
Before we dive into the sealing technology, let’s briefly review what pneumatic double diaphragm pumps are and how they operate. These pumps are positive displacement devices that use compressed air to move two flexible diaphragms back and forth. As the diaphragms flex, they create a vacuum on one side, drawing fluid in, and then expelling it on the other side. This alternating movement generates a pulsating flow, making them suitable for a wide range of applications, from transferring viscous fluids to handling abrasive slurries.
The Challenge of Sealing
Sealing is a critical aspect of any pump’s design, but it’s particularly challenging when it comes to Pneumatic Double Diaphragm Pumps. Why? Because these pumps are designed to handle a vast array of fluids, some of which can be highly corrosive or abrasive. Ensuring that no leakage occurs during operation is not just a matter of convenience; it’s a matter of safety and environmental responsibility.
Materials Used in Manufacturing Diaphragms
At the heart of the sealing technology in pneumatic diaphragm pumps are the diaphragms themselves. These diaphragms are made from various materials to suit different applications. Common materials include:
- Rubber: Rubber diaphragms are excellent for handling many chemicals and are known for their flexibility and durability.
- Teflon (PTFE): PTFE diaphragms are ideal for applications involving highly corrosive chemicals, as they are exceptionally resistant to chemical attack.
- Santoprene: Santoprene diaphragms offer a balance between chemical resistance and flexibility, making them suitable for a wide range of fluids.
The choice of diaphragm material depends on the specific fluid being pumped and its compatibility with the diaphragm material.
Dynamic Sealing
Pneumatic diaphragm pumps employ dynamic sealing to prevent leakage. Dynamic seals work by maintaining a seal while parts are in relative motion. In these pumps, the diaphragms are the dynamic seals. The dynamic sealing process can be broken down into the following steps:
1. Diaphragm Flexing: As compressed air is applied to one side of a diaphragm, it flexes and pushes the fluid out of the other side. This flexing creates a tight seal between the diaphragm and the pump body, preventing fluid from leaking out.
2. Diaphragm Reversal: When the air pressure is released on one side, the diaphragm returns to its original position, creating a vacuum and drawing fluid in from the suction side. Again, the diaphragm seals against the pump body, ensuring no leakage occurs.
3. Check Valves: In addition to diaphragms, check valves play a crucial role in sealing technology. These valves allow fluid flow in one direction while preventing it in the other, ensuring that the fluid moves in the desired direction without leaks.
Benefits of Sealing Technology in Pneumatic Diaphragm Pumps
The sealing technology in pneumatic diaphragm pumps offers several significant benefits:
1. Zero Leakage Assurance
The primary benefit, as the title suggests, is zero leakage. Regardless of the fluid being pumped, the sealing technology ensures that it stays contained within the pump, preventing any spills or leaks that could lead to safety hazards or environmental damage.
2. Versatile Fluid Handling
Thanks to the availability of different diaphragm materials, Double Diaphragm Pumps can handle a wide range of fluids, from aggressive chemicals to viscous liquids, without compromising sealing performance.
3. Durability and Longevity
The sealing technology’s robust design and the choice of durable materials for diaphragms contribute to the longevity of these pumps. They can withstand the rigors of continuous operation in demanding industrial environments.
4. Reduced Maintenance
With fewer concerns about leaks and wear, maintenance requirements are generally lower for pneumatic diaphragm pumps compared to other types of pumps. This translates to cost savings and increased uptime.
Application Highlights of pneumatic diaphragm pumps
The sealing technology in Pneumatic Double Diaphragm Pumps Suppliers in India finds application across various industries:
Chemical Industry: Handling of corrosive and abrasive chemicals without leaks is crucial for safety and environmental compliance.
Pharmaceuticals: The ability to maintain aseptic conditions while handling sensitive pharmaceutical substances is vital.
Food and Beverage: These pumps can transfer food products without contamination, thanks to their reliable sealing technology.
Mining and Construction: Handling abrasive slurry and wastewater without leakage is essential for efficient operations.
Oil and Gas: These double diaphragm pumps can handle various fluids encountered in oil and gas exploration and production without compromising safety.
Conclusion
The sealing technology in Pneumatic Double Diaphragm Pump Manufacturers in India plays a pivotal role in ensuring their effectiveness and safety across diverse applications. It’s this sealing prowess that makes these pumps the go-to choice for fluid handling in industries where zero leakage is not just an aspiration but a requirement.
As technology continues to advance, Nirmala Pumps & Equipments even innovates more innovations in sealing technology, further enhancing the capabilities and reliability of pneumatic diaphragm pumps. When selecting a pump for your specific application, always consider the compatibility of the diaphragm material with the fluid you’ll be handling, as this is a key factor in achieving zero leakage assurance.
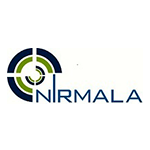
Nirmala Pumps & Equipments
Nirmala Pumps & Equipments is an Indian company that manufactures and supplies pump systems, valves, strainers, and pneumatic pumps since 1989. We provide services to different industries, both domestically and internationally, such as citrus, distilling, wastewater treatment, and petroleum.